The Power and Precision of Electric Injection Molding
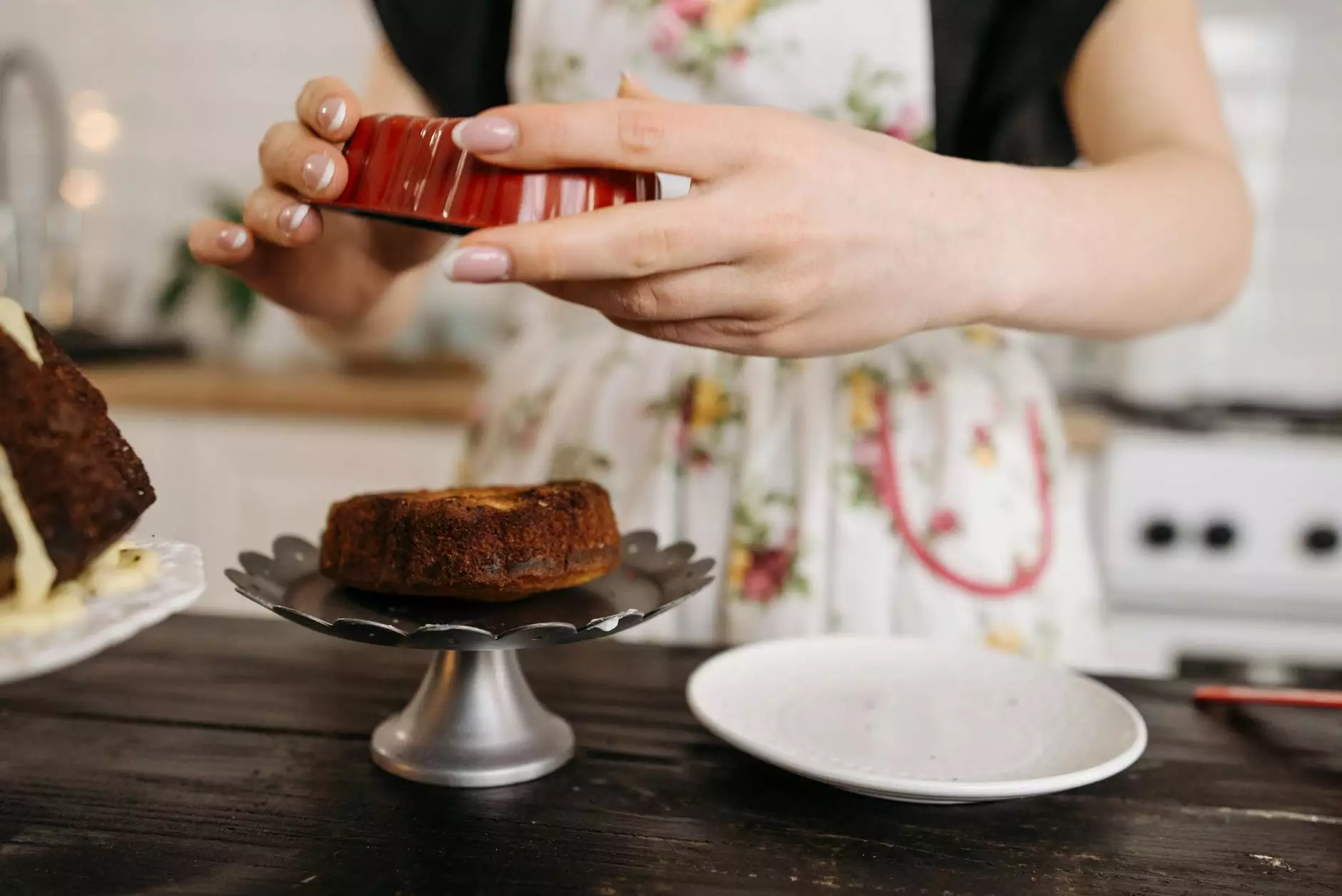
In the ever-evolving world of manufacturing, electric injection molding stands out as a revolutionary technique that combines efficiency and precision. With the growing demands of modern industries, this method has become increasingly vital in producing high-quality plastic parts. At Deep Mould, we are dedicated to producing exceptional metal fabrications, using cutting-edge technologies, including electric injection molding, to meet and exceed our clients' expectations.
Understanding Electric Injection Molding
Electric injection molding is a process that uses electric motors to drive the injection molding machine, enhancing the accuracy and repeatability of the production process. Unlike traditional hydraulic systems, electric molding provides greater control over the injection speed and pressure, resulting in improved part quality and reduced waste.
How Electric Injection Molding Works
The process begins with resin pellets being fed into a heated barrel where they are melted into a homogeneous material. The electric motor controls the movement of the screw, which injects the molten plastic into a mold cavity at high speed. After cooling, the newly formed part is ejected from the mold, ready for further processing.
The Advantages of Electric Injection Molding
Choosing electric injection molding over traditional methods offers several significant advantages:
- Enhanced Precision: Electric motors provide finer control of the injection process, resulting in precise dimensions and uniform wall thickness in finished products.
- Reduced Energy Consumption: Electric molding machines typically consume less energy than their hydraulic counterparts, translating to cost savings.
- Shorter Cycle Times: The speed of electric motors allows quicker cycle times, increasing productivity and enabling faster time-to-market for new products.
- Minimized Maintenance: Electric machines have fewer moving parts, leading to reduced wear and tear, lower maintenance costs, and longer machine lifespans.
Applications of Electric Injection Molding in Metal Fabrication
In the realm of metal fabrication, electric injection molding plays a crucial role, particularly in the production of components for various industries, such as:
Aerospace Industry
The aerospace sector demands superior quality and lightweight components. Electric injection molding facilitates the production of intricate parts that meet the rigorous standards of aviation safety and performance.
Automotive Manufacturing
In automotive applications, electric injection molding is employed to create lightweight plastic components, such as dashboard assemblies, that contribute to fuel efficiency without compromising safety.
Consumer Electronics
The rise of consumer electronics has driven a demand for compact, intricately designed components. The high precision of electric injection molding allows manufacturers to develop parts that fit seamlessly into modern gadgets.
Deep Mould: Your Partner in Quality Electric Injection Molding
At Deep Mould, we pride ourselves on our commitment to utilizing the latest technologies, including electric injection molding, to deliver products that set the industry standard. Our state-of-the-art facilities and skilled professionals ensure that every part we produce meets the highest quality benchmarks.
Why Choose Deep Mould?
- Expertise and Experience: Our team comprises seasoned professionals with years of experience in metal fabrication and injection molding techniques.
- State-of-the-Art Technology: We continually invest in advanced machinery and processes to maintain our competitive edge.
- Commitment to Quality: Every project undergoes rigorous quality checks to guarantee that our products meet or exceed customer specifications.
- Customer-Centric Approach: We collaborate closely with our clients to understand their needs and deliver tailored solutions that drive their success.
The Future of Electric Injection Molding
The future of manufacturing lies in sustainable practices and innovative technologies. As industries continue to embrace automation and smart manufacturing, electric injection molding is likely to become the predominant method for producing high-quality plastic components.
Trends to Watch
- Increased Automation: The integration of robotics and artificial intelligence is expected to streamline production processes further.
- Biodegradable Materials: With a growing emphasis on sustainability, the development of biodegradable plastics and their incorporation into electric molding processes holds great promise.
- Industry 4.0: Advancements in connectivity and data utilization will enhance machine performance and efficiency, leading to reduced downtime and enhanced productivity.
Conclusion
In conclusion, electric injection molding represents a significant advancement in manufacturing technology, offering unparalleled precision, efficiency, and sustainability. At Deep Mould, we are dedicated to harnessing this technology to deliver top-quality metal fabrications across various industries. As we look to the future, we remain committed to innovation and excellence, ensuring that our clients receive the best possible products and services.
For more information about our electric injection molding services or to discuss your specific needs, please visit us at deepmould.net.